Choosing the Best Raw Materials for Metal Stamping
Copper Alloys
Copper and copper alloys – brass, bronze, nickel silver, high performance copper alloys – are often chosen for their excellent thermal and electrical conductivity. They are corrosion resistant, antibacterial, non-sparking, and non-magnetic.
They are easy to work, and their malleability makes them a favorite for metal stamping applications. Copper and copper alloys can be drawn smaller and thinner than almost any other material, making it possible to produce extremely precise and complex shapes when stamping. However, the softness of the metal makes it unsuitable for strength applications.
Key Characteristics:
- Electrical and thermal conductivity: Second only to silver in terms of conductivity and far more cost-effective, copper is a common alloy metal in electrical and HVAC applications.
- Ductile and malleable: Even after hardening, copper remains ductile and easy to work. Wires and tubes commonly use copper as a raw material.
- Durable: Sunlight and cold temperatures do not cause copper to become brittle, allowing it to be used across a wide temperature range.
- Corrosion resistant: Copper is relatively resistant to corrosion as it forms a stable oxide layer on its surface. It can be alloyed with other metals to further improve its corrosion resistance.
- Sanitary: Copper has antimicrobial properties and is easily sanitized, making it suitable for the food processing industry.
- Finish: Copper and copper alloys offer a variety of beautifully colored finishes, making them popular for architectural features and consumer goods.

Steel Alloys
Steel and steel alloys are versatile, economical, and relatively strong, making them the workhorse of the mechanical world and suitable for a good proportion of metal stamping for general applications. Steel’s strength comes at the cost of weight, as steel alloys are quite heavy and dense.
One of steel’s great benefits is that it can be alloyed with other elements and treated either before or after stamping. There are steel alloys specifically designed for strength, toughness, corrosion resistance, and more. A soft, malleable steel alloy can be stamped into a complex shape, then heat treated afterwards to increase its hardness.
Stainless steels – while more expensive than carbon steels – are highly resistant to corrosion and have an attractive finish. Alternatively, galvanizing offers a more economical way to protect steel parts from corrosion.
Key Characteristics:
- Price: Steel and basic steel alloys are some of the most price-competitive raw materials available.
- Strength: Strong and sturdy, steel is a key material for the construction industry.
- Workable: Steel takes well to stamping, machining, forging, welding, and many other manufacturing processes.
- Versatility: There are steel alloys adapted to all kinds of purposes and applications. Heat and corrosion treatments further expands options.
- Corrosion resistance: (for stainless steel) Stainless steel is naturally resistant to corrosion and frequently used in the food processing and medical sectors.
- Magnetic: Most (but not all) steel alloys are magnetic. Stainless steel is a notable exception.
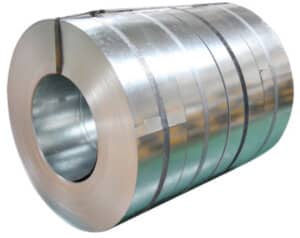
Aluminum Alloys
For applications that require strength without the heavy weight, look for aluminum alloys. One of the lightest metals used commercially, these alloys are frequently used in the transportation industry where any weight reductions that might contribute to fuel savings gives an advantage.
While aluminum alloys cost more than steel alloys, the metal’s natural corrosion resistance and light weight mean that parts last longer and can be made from much less raw material. Flexible and malleable, metal stamping can form aluminum and aluminum alloys into complex geometrical shapes.
Aluminum has high thermal conductivity, but equally high reflectivity. Heat will be transmitted quickly from a source in direct contact, but reflected from sources at a distant, which means aluminum alloys can work as an insulator. This metal is non-magnetic.
Key Characteristics:
• High strength-to-weight ratio: Extremely light yet strong, aluminum alloys are common alloys within the aerospace, automotive, and construction industries.
• Malleable and flexible: More elastic than steel, aluminum can be drawn and stamped into more complex shapes.
• Corrosion-resistant: Aluminum surfaces immediately form a protective oxide layer on contact with air, protecting fabricated aluminum parts from rust.
• Finish: Aluminum and its alloys have a shiny and smooth decorative finish that requires little maintenance.
• Thermal and electrical conductivity: Aluminum is only 60% as conductive as copper, but is also only a third of the weight.
• Low temperature resistance: Aluminum remains strong at low temperatures, whereas steel alloys may become brittle.
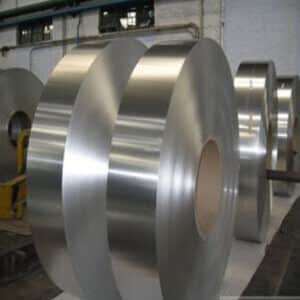
Material Thickness Tolerance – The chart below lists standard tolerance for cold rolled coil and sheet steel. Tighter tolerance can be achieved through secondary rolling although this adds to cost, lead time and results in larger minimum material buys.
Gauge | Min. | Max. | Nom | lbs/sqft |
---|---|---|---|---|
10 | .1285 | .1405 | .1345 | 5.624 |
11 | .1136 | .1256 | .1196 | 5.001 |
12 | .0986 | .1106 | .1046 | 4.374 |
13 | .0847 | .0947 | .0897 | 3.751 |
14 | .0697 | .0797 | .0747 | 3.124 |
15 | .0623 | .0723 | .0673 | 2.814 |
16 | .0548 | .0648 | .0598 | 2.501 |
17 | .0498 | .0578 | .0538 | 2.250 |
18 | .0438 | .0518 | .0478 | 1.999 |
19 | .0378 | .0458 | .0418 | 1.748 |
20 | .0329 | .0389 | .0359 | 1.501 |
21 | .0299 | .0359 | .0329 | 1.376 |
22 | .0269 | .0329 | .0299 | 1.250 |
23 | .0239 | .0299 | .0269 | 1.125 |
24 | .0209 | .0269 | .0239 | 0.999 |
25 | .0179 | .0239 | .0209 | 0.874 |
26 | .0159 | .0199 | .0179 | 0.749 |
27 | .0144 | .0184 | .0164 | 0.686 |
28 | .0129 | .0169 | .0149 | 0.623 |